Blade Care
Info. & Technical
SHORT VERSION
For people too busy to read (or learn)
NEVER allow the cutting tip of a blade to touch anything except the material you wish to cut.
If you want to know why then read below.
THIS INFORMATION IS FOR YOUR BENEFIT - NOT OURS.
Damaged blades cause us no problem whatsoever.
They increase our income - at your cost!
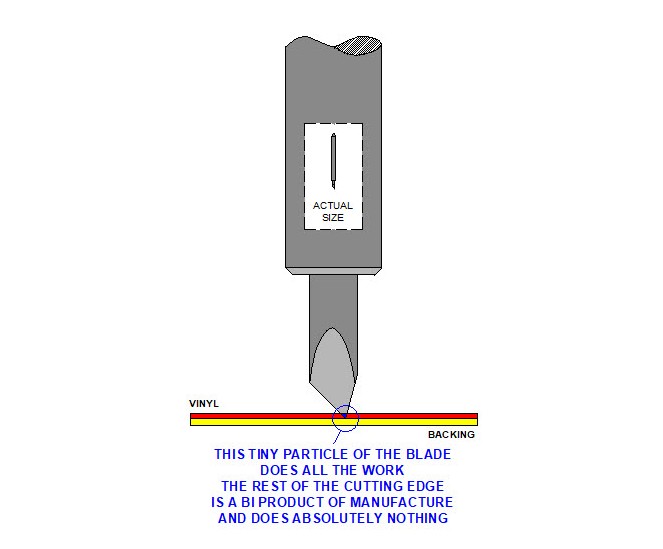
ALL plotter blades are surprisingly fragile. (not just ours)
In the enlarged illustration of a typical plotter blade you can see that ALL the cutting is done by the TINY particle shown coloured blue - its actual size is smaller than this full stop ( . )
It is VERY fragile and VERY easy to damage
You won’t be able to see the damage without a microscope.
You won’t know it is damaged until you try to weed a badly cut job.
Damage that can only be seen under a microscope can cause a blade to cut badly, or not at all.
If damage (usually chipping) can be seen without magnification it is seriously damaged.
Users do not usually have microscopes so when blades fail to cut correctly they assume they have worn out.
We see those blades under microscopes and far too many have NOT worn out they have been accidentally damaged.
Good for us - but bad for customers
We see those blades under microscopes and far too many have NOT worn out they have been accidentally damaged.
Good for us - but bad for customers
When we see it we advise customers how to avoid it in future.
YOUR PLOTTER IS ONLY AS GOOD AS THE BLADE
We already use the highest quality (and most expensive) tungsten carbide available.
There is very little more we can do to extend blade life but there is much you can do.
If you wish to cut accurately and prolong the life of your blades you should to treat them with care.
Damaged blades can cost you more than you might think.
Extra weeding time and wasted material can cost you many times more than the cost of a blade.
If you want to know how to avoid damage you will find some useful information below.
If you are not interested we will be happy to take the money you may waste.
But we won't be there to help you to weed badly cut jobs.
Why are plotter blades so easy to damage?
With some very rare exceptions plotter blades are made from Tungsten Carbide, which although it is one of the hardest and most wear resistant materials known to mankind, is also one of the most brittle (almost like glass) especially when it is ground to the very fine edge needed for cutting vinyl and similar materials.
We manufacture them, and where appropriate, re-sharpen them accurately to within a few microns, we examine them under microscopes then carefully protect the tips and post them to customers in padded envelopes.
But despite all our efforts many will be damaged by careless (or untrained) users before they ever cut anything.
Taking care of your blades.
When installing a new blade or Smart Knife in your plotter always start with a LOW pressure/force and do a test cut.
If the initial cutting pressure is set too high your blade will penetrate the backing paper and be damaged by the cutting strip or roller underneath. (this can also damage your plotter).
If you make that mistake the damage is instant, there are no second chances.
Reducing the pressure after the damage has occurred is pointless (so is the blade) which will then cut badly or not at all.
Avoid false economy.
Saving pennies to lose pounds.
Avoid using scraps of media with damaged or uneven edges that can drop out or catch and damage the blade when your plotter is initialising.
DO NOT remove knife assembly from plotter unnecessarily.
Accidentally touching blades on parts of your plotter during removal and refitting provides opportunities for damage.
DO NOT leave blades unprotected - even when only temporarily removed from your plotter.
Blades should always be stored separately with tips protected.
Cutting tough, thick and/or abrasive materials.
Reflective, fluorescent, foil, card, magnetic, polyester, polycarbonate, Lexan, Lexedge, Mylar etc
A blade used on some of these materials can lose the extreme sharpness needed for finer materials.
Use a separate blade - sometimes - but not always - a different type - but always separate.